‘FOUP’ Handler For Semiconductor Wafers
Throughout the semiconductor production process,devices are initially developed on a thin disc of silicon (normally…
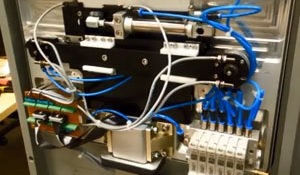
Read case study
Throughout the semiconductor production process,devices are initially developed on a thin disc of silicon (normally…
December 2023 TestWorks has been acquired by RailSense Solutions Ltd., specialists in IoT devices for…